How is Cardboard Recycled? The cardboard recycling process in 7 key steps
Cardboard is one of the most widely recycled materials in the world. This guide will showcase the seven key steps of how cardboard is recycled, showing the journey of cardboard from waste collection, right through to its new life.
Recycling cardboard helps protect the environment and saves valuable resources from landfill. Understanding the recycling process is key to ensuring that cardboard is stored and collected correctly, reducing contamination, and helping to enable a circular economy. Our Recycling, Paper and Packaging divisions at DS Smith work together to achieve this every day.
Step 1: Cardboard sorting and storage
Cardboard is used as a valuable resource for packaging across many industries, such as retail, manufacturing, print and publishing, paper mills, automotive, public sector and pharmaceuticals. Cardboard is primarily used for three purposes: Transit packaging, shelf packaging and product packaging. Product packaging can also often find its way into our homes, for example, when you buy something in-store or online. Once the cardboard has been used, it’s ready to be collected and recycled.
To make the boxes into new packaging, we need to ensure the cardboard is kept separate from any other materials. This is called Source Segregation and keeps the material clean and free from contamination.
Did you know? When cardboard is mixed with other materials for recycling, like plastics, food, or glass, as much as 20% of what is collected can be unusable due to contamination. When cardboard is stored separately however, this figure be as low as 1%.1
When cardboard is mixed with other materials, as much as 20% can be unusable!
When cardboard is stored separately, this figure can be as low as 1%!
Step 2: Managing the quality of cardboard at the recycling facility
Next, cardboard is collected and taken by delivery vehicles to a recycling facility. Here, the cardboard is checked for any contaminants, such as food or plastic, before it’s baled for transport.
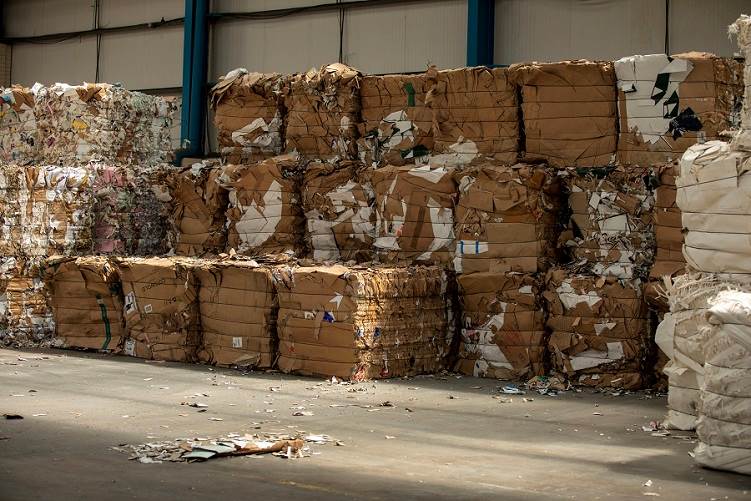
Step 3: Transportation to paper mills
Bales arrive at one of our paper mills, in loads of around 25 tonnes to fuel our paper-making process. Our largest mills are capable of processing up to 3,000 tonnes of recyclable material a day. That’s nearly 120 articulated lorry loads.
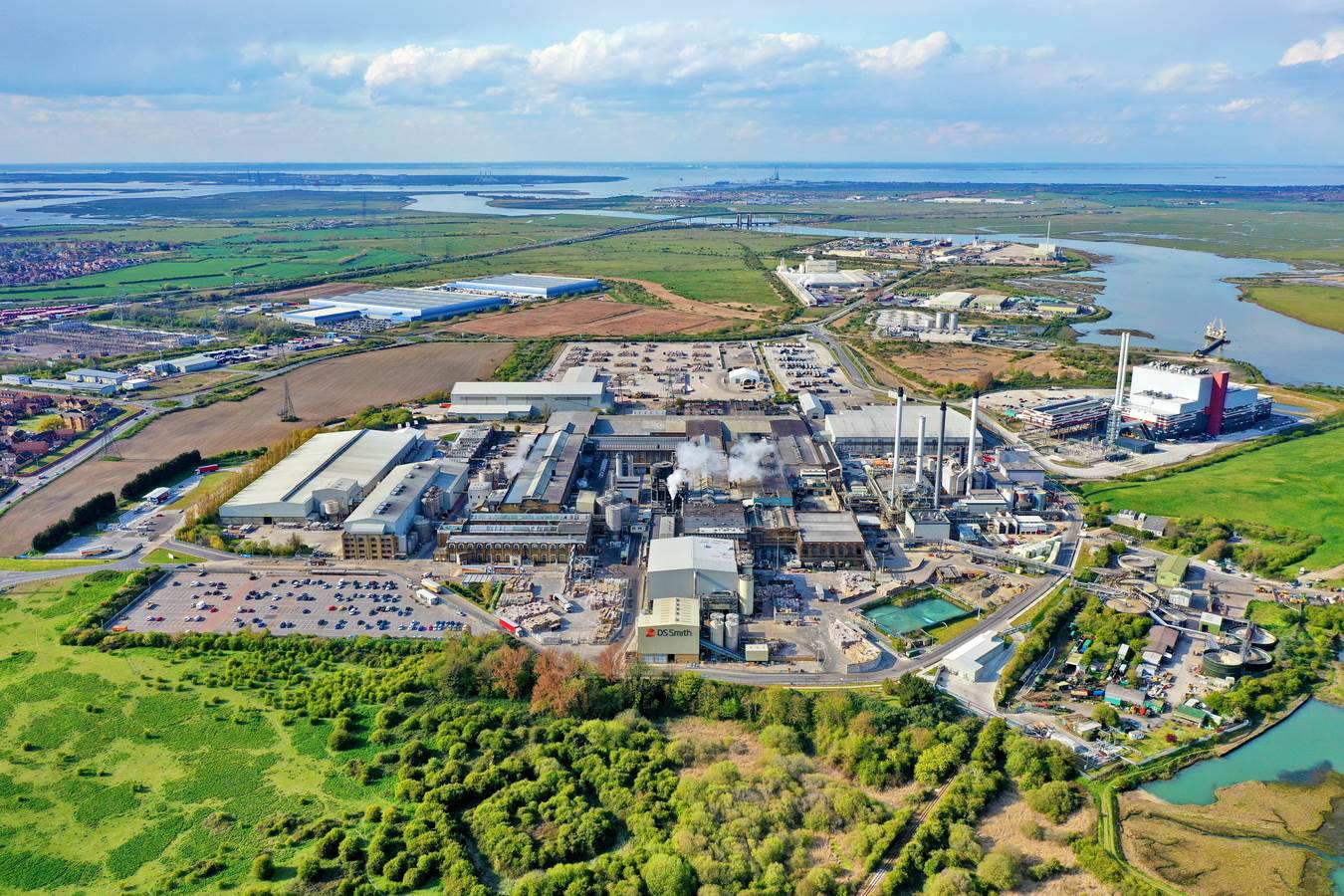
Step 4: Processing the cardboard bales to pulp
Cardboard enters the pulper, where it is mixed with warm water, breaking down the cardboard and causing the fibres to separate from each other. Any residual contaminants, such as staples, tape or plastic film are removed out of this mixture, using a combination of cleaning and screening techniques.
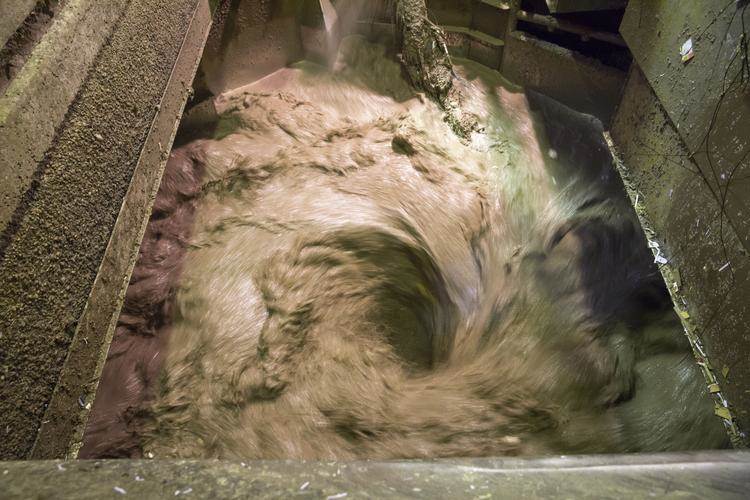
Step 5: Making the paper
The diluted fibres are formed, pressed and dried into paper at high speed on a large machine. The paper is then wound into large reels of finished paper.
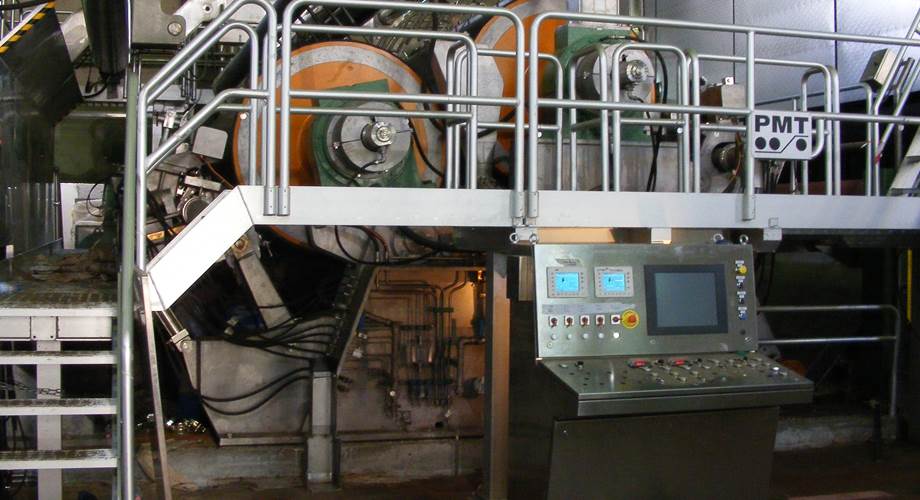
Step 6: Creating the paper reels
The paper is then wound onto a huge reel. The reels are then cut down and shipped to a packaging plant, where they will be made into cardboard.

Step 7: Creating the cardboard
At the packaging plant, the paper is fed into the corrugator, a machine that makes cardboard by fusing layers of paper together. This is usually a top and bottom layer, with several corrugated sheets in the middle.
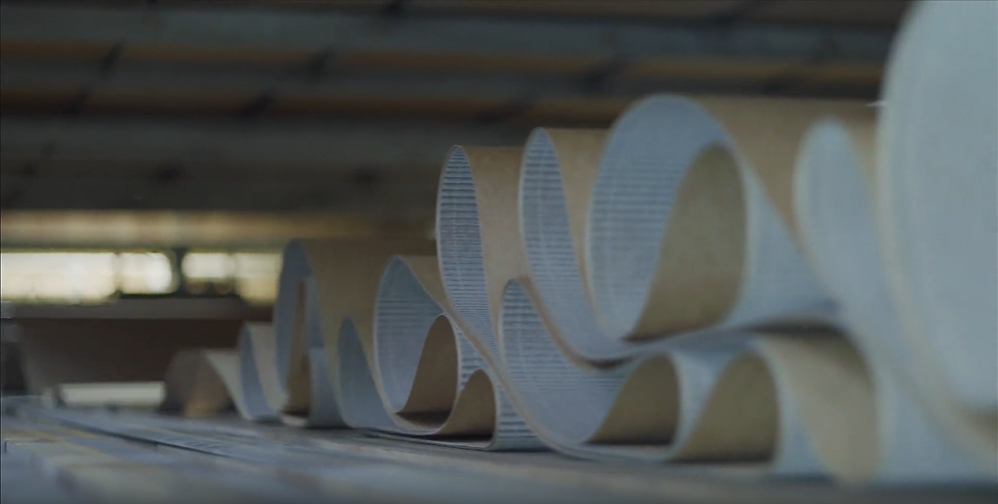
The new cardboard sheets are stamped with cuts and fold lines ready to be made into a wide range of products, including packaging, point of sale displays, and more. At this point, any necessary branding or product information will be added. Then, they are flat-packed and transported to a factory, where they are popped into shape. The cycle begins again.
Across DS Smith, this story unfolds every day, creating a sustainable solution for our customers, our business, and our environment.
Why we recycle cardboard
It is important for both domestic households and businesses to boost their recycling efforts.
Increases in recycling rates will result in fewer valuable resources being sent to landfill or incineration. By recycling more cardboard, we can keep paper fibres in the circular economy for longer. This, in turn, leads to a reduction in the demand for ‘virgin materials’, such as trees that are typically used in the production of new cardboard.
Sources:
1 European Commission: 070201/ENV/2014/691401/SFRA/A2